If you think it’s tough being a retail jeweller today, spare a thought for Pierre Bézier. A pioneer of CAD software, the French engineer did some of his most important work in a prisoner of war camp in 1940s Germany. Bézier’s ground-breaking research – originally for the car industry – went on to be adapted in everything from space travel to dentistry.
Today, computer-aided design and computer-aided manufacturing, commonly known as CAD/CAM, is no longer confined to science and industrial applications; it’s also becoming synonymous with jewellery design.
Times are a-changin’
It wasn’t long ago that jewellers saw CAD/CAM as a threat to business or, as Chris Hill, 3D product manager at supplier LST Group puts it, “A jeweller’s dirty little secret.” Today, the cutting-edge software and manufacturing technology is recognised as the perfect complement to a jeweller’s bench top.
“CAD/CAM is at the forefront of a successful business,” Hill says. “Today, the trend is to bring the CAD software out front to engage with the customer and offer 3D-printed plastic models for a trial fit.”
Trevor Sim, director of Clayfield Jewellery, has been doing just that. “Clients these days are savvy; they love to embrace the technology and interact in the design process. The sales increase has also been unforeseen,” Sim says.
Ben Farago is production manager at manufacturing company Rapid Casting. He says jewellers now want in-house CAD/CAM tools.
“As more jewellers are exposed to CAD/CAM, they know when a project would benefit from it,” Farago explains, adding, “It’s now quite common to have a low-cost 3D printer in small workshops.”
One of the best ways to combine technology with craftsmanship is by making component pieces, according to Grant George, operations manager at metal refiner and supplier Morris & Watson.
“A jeweller will use castings to do three or four settings separate of the shank, then put it together with a laser welder,” George says. “No solders required, and you’ve got a top-class product that looks 100 per cent handmade – it’s almost impossible to tell because it’s so well done.”
Jason Tran, CAM team leader at Pallion agrees that the popularity of ‘component design’ is on the rise: “With CAD/CAM, the shank can now be drawn and printed to minimise loss, while still allowing for the setting to be handmade.”
According to Darren Sher, director of casting and refining house Chemgold: “Handmade jewellery is still going strong as our stock gauge and solder sales have increased. It’s fantastic to see traditional bench and new technology being used side by side.”
Another reason why jewellers are embracing the technology is to help them compete against the flood of generic, mass-produced goods in chain stores.
Stapleton Jewellers is a second generation, family-owned jewellery store that has been in business since 1972.
John Stapleton says that CAD/CAM has helped them to “thrive and survive in these changing times”. “As a small jewellery retailer in a shopping centre, we are able to profitably take on work that others show no interest in,” Stapleton explains.
Hill agrees, adding, “A good jewellery-specific CAD software and in-house 3D printer enables the jeweller to deliver something unique. They can quickly generate interest on new designs through social media, adapt to trending fashions and lower overheads with less stock, all at a competitive price with enough margin to make it worthwhile,” he says.
Technology improvements
Like all technology, CAD/CAM is always improving. As CAD software becomes easier to use, it attracts more jewellers willing to learn it.
“The price of these technologies plus wait times and print costs have all reduced,” Tran says. “This has opened the technology up to those that may have shied away in the past.”
Perhaps ironically, CAD/CAM has helped bring manufacturing back home to Australian soil.
The computer automation reduces the need for outsourcing labour.
“Labour is very expensive here, so CAD/CAM has been a great help for jewellers to achieve more with fewer resources,” Sher explains, adding, “They can get extra assistance without increased staff or inventory costs.”
Stapleton agrees: “Turnover is quicker and faster than if we were outsourcing overseas. Customers like to wear original jewellery and are proud to recommend where it came from.”
Stapleton says he often purchases non-standard-sized, coloured stones because they are more affordable. This means jewellery pieces need to be adjusted for the stone size, which is easy with software. “We use CAD to easily re-size a setting, fitting in with our current designs,” he explains.
Clayfield Jewellery has also saved time with CAD/CAM. “If a client’s engagement ring requires a contour fit, we have the ability to import a 3D scan of the piece,” Sim says. “Instead of spending hours recreating that ring in Matrix to then design the wedder around it, the ring is in the software in 10 to 15 minutes– a saving of many hours at the computer, and ultimately a saving of dollars for the client.”
Hill says 3D printers have been a “game changer” for many jewellers, particularly the Form 2 model from Formlabs. “It can print as many as 50 rings at a time or larger pieces like bangles, necklaces, brooches and watch cases – the cost of a ring can be as little as 10 cents in material,” Hill asserts, adding, “Standard resins can be used to prototype and test designs or offer a trial fitting so clients can buy with confidence. The Form 2’s precision produces a better surface finish, resulting in less polishing and metal loss.”
Suppliers agree that demand for 3D printers is steadily increasing, thanks to affordability. “Improvements in 3D-printing technology mean there are more low-cost 3D printers on the market,” Farago confirms. “Due to the increased reliability and user friendliness of these machines, jewellers are seeing it as an effective tool to take control of their manufacture and keep it in house.”
Anthony Nowlan, director of jewellery technology company Evotech Pacific, says there’s plenty to be excited about in the software realm.
Suppliers weigh inWhat will CAD/CAM look like in 2022? 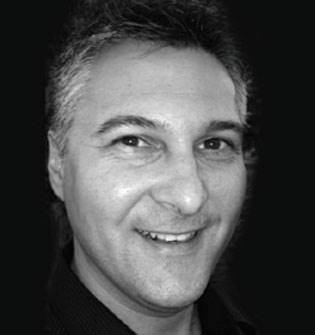 “I think we’ll see a decrease in rapid prototyping, in exchange for rapid manufacturing. Direct to metal manufacturing is not only advancing to create higher resolution pieces quicker than before, but is also falling in price.” - Anthony Nowlan, Evotech Pacific | 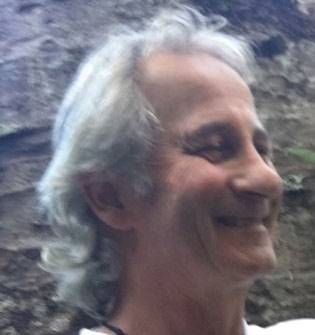
“Sooner or later casting will be gone, and we’ll just be printing directly. I imagine going forward there will be a big choice of design libraries too.” - Grant George, Morris & Watson | “To remain competitive, many jewellers will need to embrace CAD/CAM by outsourcing the design aspect to companies like Chemgold, or learn to use the software themselves. Direct metal printing could also be an option by 2022 if it becomes economically viable.”
- Darren Sher, Chemgold | 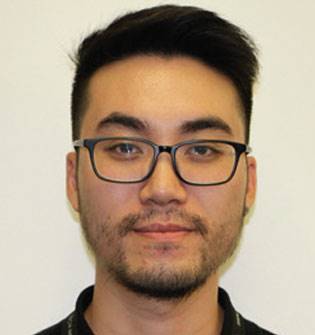
“Direct metal printing will be the norm. Designs will be realised in shorter lead times, and creations will be made available digitally to the client, who will then be able to wear the piece through virtual reality before proceeding with the make.” - Jason Tran, Pallion | 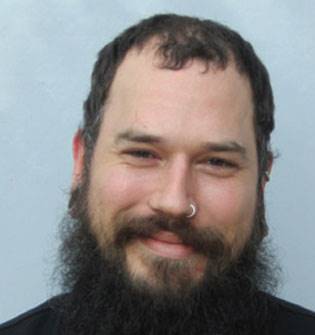 “There are no real limits to what might be achieved with CAD/CAM in the future. By 2022, there will probably be commercially viable, high-resolution direct-to-precious-metal 3D printing.” - Ben Farago, Rapid Casting | 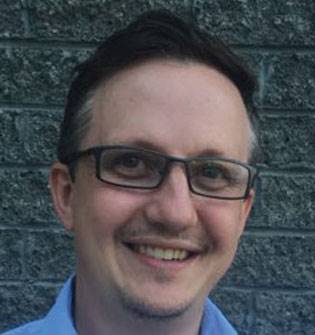
“By 2022 we will see a very different landscape of brands in the 3D printing market. There is huge investment in research and development in the race to deliver new 3D print advancements, at a fraction of the original cost.” - Chris Hill, LST Group |
|
“The Matrix V9 software has introduced new tooling, which assists in quicker design times without compromising on quality,” Nowlan begins. “Counter Sketch International software is regularly updated with improvements and new pieces to its libraries, and ZBrush has just released its 2018 upgrade, which I believe is more intuitive than before. It also contains powerful tooling for digital sculpture.”
The power of bespoke
It’s not just software and printer prices that have improved; jewellers’ creative talents have also gained an edge with CAD/CAM.
“Having CAD/CAM can really set the smaller independents apart from the chains who can’t provide the specialised service,” Sher says.
Such exciting possibilities have helped jewellers regain their creative mojo, according to Hill.
“3Design CAD software and Formlabs 3D printers have reignited the passion to create beautiful, quality pieces,” he says.
Stapleton relates a recent success story when he helped a client create a piece with “her memories and her own gold”. Using CAD software, he re-modelled three old diamond rings into one. “We were able to email her the renderings, then reproduce the model in resin with a 3D printer before handmaking the final ring,” he explains.
Farago believes CAD/CAM has helped boost retailer confidence and, subsequently, success. “Some of our CAD/CAM customers have produced award-winning work at the national and international level,” he notes. “The great thing with CAD is the more someone uses it, the better they get at it. As they become more confident, their designs become more interesting and elaborate. We see customers improve their design work and develop a distinct style as their confidence grows.”
Tran is another supplier to attest to “truly extraordinary” client designs. “Men’s rings in particular are just jaw-dropping in their creativity and individualism,” he says. “Not because an artisan jeweller could not have made them previously, but because they now have a greater palette of design and production options available to them.”
Nowlan says his clients are mostly small businesses who use CAD not just for custom makes but also for ‘bread and butter’ pieces. “The type of pieces that might take a few hours on the bench to make but only a fraction of that time in Matrix or CSI,” he explains.
Sher gives a practical example: “An elaborate design that may take eight hours by hand could potentially be drawn in half the time using CAD, and you also have no excess metal. Finally, the design and model may be duplicated whenever required.”
Retailers weigh inHow has CAD/CAM improved business? 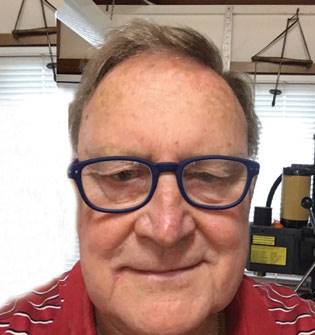 “CAD/CAM has allowed the business to thrive and survive in these changing times. Making earrings with CAD is fantastic, as one earring is mostly a reverse of the other. Hand making them is so time [and cost] consuming. Sales turnover is quicker and faster than if we were outsourcing overseas, because of price alone.” - John Stapleton, Stapleton Jewellers | 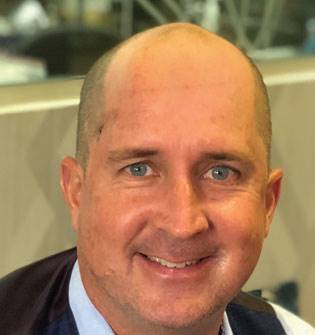
“CAD is the single biggest thing that has enabled us to grow our business. Along with 3D printing and 3D scanning– which is all done in-house– we are able to offer the client a full design suite. With the help of CAD and other technology we remove the doubt in a client’s mind prior to manufacture, by offering the desired design in real life.” - Trevor Sim, Clayfield Jewellery |
|
Tips for success
Can automation ever completely replace the human touch? Farago says that realistically, the power of machines still have certain restrictions.
“People think it’s as easy as turning on a printer and pressing print but there’s a lot of trial and error to get CAD/CAM to work effectively. If bureaus or jewellers aren’t willing to put the time in, the results will show in the end product,” he warns.
On the flip side, being too good at CAD can create problems too.
“It’s quite easy to draw something that would be impossible to cast,” George explains, adding that he has seen designs come to Morris & Watson with features far too delicate, that would snap off a physical mould.
According to Tran, the solution is to work closely with the experts: “How a piece is drawn will directly influence how successfully it will cast. The key is to work alongside your casting provider as they are best placed to advise on technical aspects of the design and draw process – some designs may be better suited to printing in wax than resin.”
Nowlan cautions jewellers to avoid cutting corners when investing in CAD/CAM, putting it succinctly: “just like diamonds, you get what you pay for.”
“You can design jewellery in any CAD software but going the cheapest route is not always the wisest financial decision; software such as Matrix or CSI have been designed with the jeweller in mind,” he explains.
However, Sher assures that any jeweller can eventually graduate to independent CAD/CAM work if they want to: “Once the customer is comfortable with the design process and is doing more volume, we would recommend they consider purchasing the CAD software themselves.
We would happily provide guidance on the best software for the customer based on their budget and needs.”
To infinity and beyond
The future is bright for CAD/CAM – and for jewellers who stay on board with this innovative technology.
As Hill points out, other industries are already demonstrating what’s ahead, and it’s good news. “CAD technology in other markets has witnessed huge changes over the past few years,” he says. “The change is not in the products themselves but in how they are delivered, which has made them far more accessible. The major players developing CAD solutions for jewellers will inevitably be going down this path.”
Evotech Pacific offers CAD/CAM training for jewellers. In addition, the company is about to launch an online marketplace that will provide a range of services, including interacting with bidders for manufacturing jobs. “Jewellers who perhaps don’t have their own CAD software or are more comfortable using a service bureau can sign up and upload sketches along with descriptions,” Nowlan says of the website. “This information is shared with every designer in the marketplace, who will be able to provide a quote for the job.”
Chemgold’s library of classic styles, JewelMount, also provides a simple starting point for newcomers. “All they need to do is advise what aspect of the design they wish to modify, such as changes to the stone and shank dimensions, mixing shanks and settings, or adding extra stones,” Sher says.
CAD/CAM possibilities remain endless. As Farago enthuses, “There are no real limits to what might be achieved with CAD/CAM in the future. In the short term, we will probably see higher resolution and lower-cost wax printers – the main benefit being that all resin-related casting issues would be eliminated without losing resolution.”
Though conditions may be tough for jewellers, exciting times are ahead for those that embrace change.